- Sustainability Report 2021-2022
- Planet
- Materials management
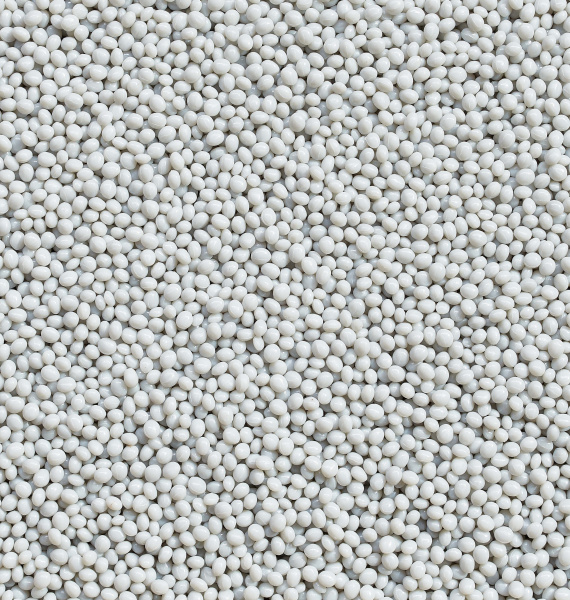
We understand the potential negative environmental and social consequences of the plastics industry. We have therefore started to engage with our suppliers to support their sustainability journey. The ALPLA Group’s supplier code of conduct – mandatory for all our suppliers – as well as the supplier self-assessment contain the main principles and international standards we adhere to and promote them to our suppliers.
Below we present in detail the volume of our raw materials; other purchased materials (including colouring and additives, as well as secondary packaging used in production) account for only a negligible fraction compared to the raw materials and are hence not elaborated on. Our raw materials are predominantly purchased from external suppliers, apart from some of the recycled raw materials used which are provided by our own recycling plants.
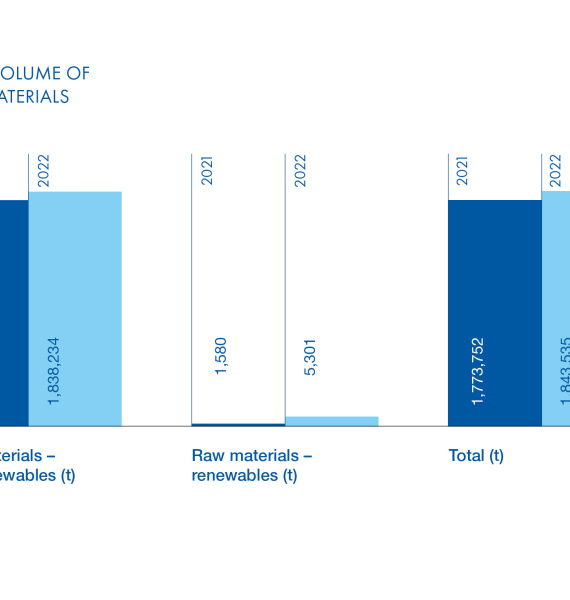
The total volume of the raw materials saw a 4% increase year-on-year. The volume of plastics from renewable sources (i.e. bio-based materials) increased significantly, although these still only accounted for 0.3% of the total volume in 2022.
Material consumption based on plastic type was similar in the two reporting years: we primarily processed PET (54.9% in 2021, increased to 57.2% in 2022) and HDPE (38.6% and 36.4%, respectively). PP accounts for the remaining share in the mix of non-renewable raw materials.
The circular economy and recycling
The circular economy has always been at the heart of ALPLA’s strategy, and we are actively working on the 4Rs of the circular economy as follows:
-
Reduce: Our initiatives include numerous cooperations with clients to achieve lighter products (using less material). A prime example of this is our SIMPLE ONE, an ALPLA refill solution made of 100% recycled HDPE, with 80% of material savings due to extremely lightweight packaging, resulting in a 55% GHG emission reduction as compared to a similar glass bottle. We also have 68 in-house operations worldwide. This form of cooperation enables various environmental benefits. For instance, there is no need for transportation or transport packaging, thus reducing the associated GHG emissions and secondary packaging material needed. In 2022, our in-house plants saved around 120,000 tonnes of CO2e compared to the scenario of these being base plants.
-
Reuse: In 2021, we partnered with Vöslauer to produce a reusable PET bottle made of fully recyclable PET and containing around 30% recycled material. According to the analysis by c7-consult, the reusable Vöslauer bottle causes only 70% of the carbon emissions of alternative reusable glass bottles, making it the more environmentally friendly packaging solution. Another example is the PET pearl bottle well-known in Germany – a reusable solution for the ‘Genossenschaft Deutscher Brunnen’, the main purchasing association of the German mineral water industry, with 30% recycled content. Reusable PET bottles from ALPLA are also available in other countries, such as Mexico. With European legislation promoting the use of reusable bottles, we plan to scale up these operations in the future.
-
Replace: Paper, plant-based or bacteria-derived materials – ALPLA is thinking outside of the crude-oil-based box, in search of the optimum packaging solution for the future with numerous joint venture partners. Our activities for replacement focus on different – albeit somehow interrelated – topics. In 2021, with the acquisition of a significant minority stake in the Slovakian company Panara, focusing on fully bio-based and biodegradable plastics, we stepped up our ambitions to substitute crude oil with bio-based plastics. We also introduced our biodegradable packaging solutions under the Blue Circle Packaging label: our first product is the Blue Circle home-compostable coffee capsule. Furthermore, we have been a partner of Blue Ocean Closures since its foundation in 2021, targeting the acceleration of the development of bio-based, biodegradable and recyclable caps and lids. Finally, we have been active in the development of paper bottles under our brand Paboco since 2019. Together with our pilot customers, Paboco is working intensely on realising its long-term objective: the development and scaling of a fully bio-based, recyclable, fibre-based bottle made of renewable materials.
-
Recycle: We have been involved in the recycling of plastic and the processing of the recycled material into new packaging for more than 30 years, advocating the bottle-to-bottle approach, meaning that plastic bottles should not be regarded as waste but rather as valuable materials that can be turned into new bottles. This approach not only generates value for used plastic packaging, thus stimulating the circular economy and preventing littering, but also has a considerable impact on GHG emissions, as recycled PET (or rPET) causes up to 90% fewer GHG emissions during its life cycle than the same amount of virgin PET, while maintaining the excellent characteristics of a PET bottle from virgin materials.
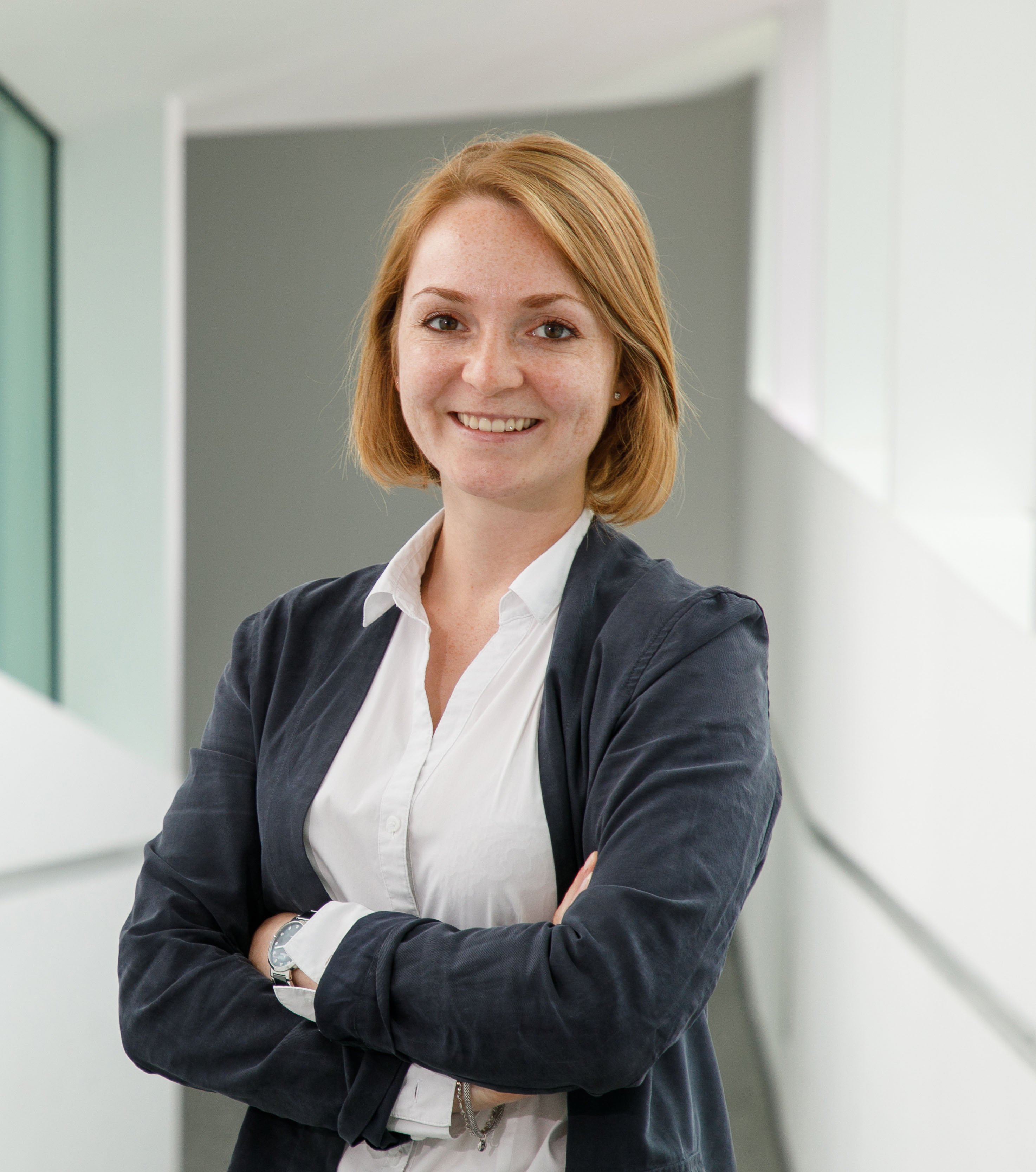
Lisa Blum
Recycling Expert
‘Recycling is not the conclusion of a packaging life cycle, but rather its inception. While recycling plastic bottles represents one facet of the broader circular plastics economy, ALPLA is leading the way as a best-practice pioneer with substantial expertise.’
Our initiatives clearly showcase our determination to be a global recycling champion:
-
Design for recycling: All packaging produced should be designed in such a way that the recycled material has the highest possible chance to be reused. This can be achieved by reducing the complexity of all packaging as much as possible without compromising on functionality or consumer safety. For ALPLA, this means that the packaging we produce is designed to be fully recyclable, allowing it to be used to create new packaging.
-
Increasing recycling capacities: While our first steps into recycling were taken a long time ago, the number and the installed and projected recycling output of recycling plants within ALPLA considerably increased during the reporting years. In 2021, we expanded our plant in Anagni, Italy, with an annual capacity of 15,000 tonnes for PET recycling, complemented with another 15,000 tonnes in Targu Mures, Romania (as part of a joint venture). Two acquisitions in Germany further increased our global PET recycling capacity by an annual 42,000 tonnes. In Mexico, we opened a new plant in 2021 that focuses on the recycling of HDPE (with an annual capacity of 30,000 tonnes), while we also initiated a PET recycling plant together with Coca-Cola FEMSA in 2022 (35,000 tonnes annual capacity). Finally, in 2022, as a joint venture with PTT Global Chemical, we opened a recycling plant in Thailand that has an annual production capacity of 45,000 tonnes of recycled PET and HDPE, now one of the largest recycling plants for these plastics in Asia.
-
Ellen MacArthur Foundation membership: We are a signatory member of the New Plastics Economy’s Global Commitment, an initiative of the Ellen MacArthur Foundation (EMF). As part of this commitment, we have set numerous targets related to recycling. For example, we have committed by 2025: to have all our produced packaging products be 100% recyclable (89.3% in 2022), to invest 250 million EUR in recycling activities (74.5 million EUR in 2022) and to reach 25% post-consumer-recycled (PCR) raw materials in our products.
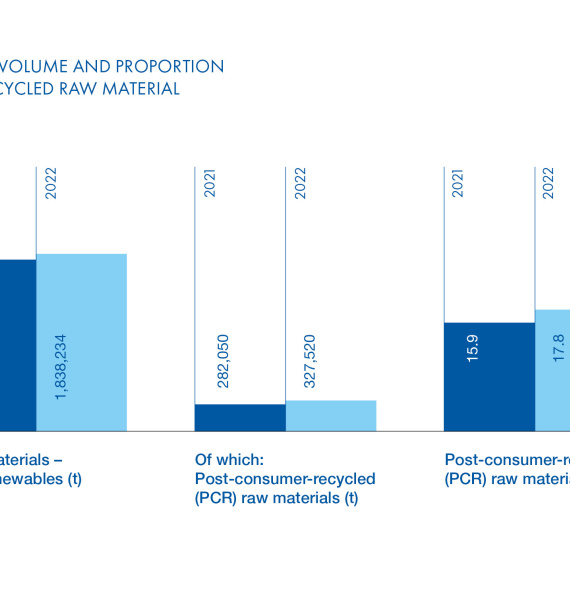
The proportion of recycled materials increased significantly in the reporting period, in line with our strategic objectives. In 2021, we purchased approximately 282,000 tonnes of recycled plastics (of which 68% was PET), which equates to 16% of all the materials purchased. In 2022, this increased to 327,520 tonnes (68% PET), which equals 18% of the overall consumption.
Waste management
Our focus on circularity is also reflected in how we manage our waste during operation. All plastic scraps arising from production are recycled and subsequently channelled back into the loop, while we also sell scrap materials that are not recyclable within our production process. We distinguish between hazardous waste (cleaning chemicals, oils, batteries, paints, etc.) and non-hazardous waste (municipal waste, packaging waste, construction and demolition waste, etc.) when collecting data from our plants. We are currently working on an update of our waste data management and will therefore disclose our waste generation and treatment figures in our next sustainability report.
Challenges
Waste collection
While our complex recycling process covers the steps all the way from aggregating unsorted household waste to the extrusion and decontamination of (ground, washed and sorted) flakes, waste collection is out of our scope. Unfortunately, due to the lack of efficient waste collecting systems in numerous countries worldwide, a considerable proportion of plastic packaging still ends up in landfills or is incinerated instead of being kept in the loop for recycling. States should therefore invest in intelligent waste management systems and ban landfilling/incineration of recyclable plastic packaging, as what is not collected cannot be recycled.
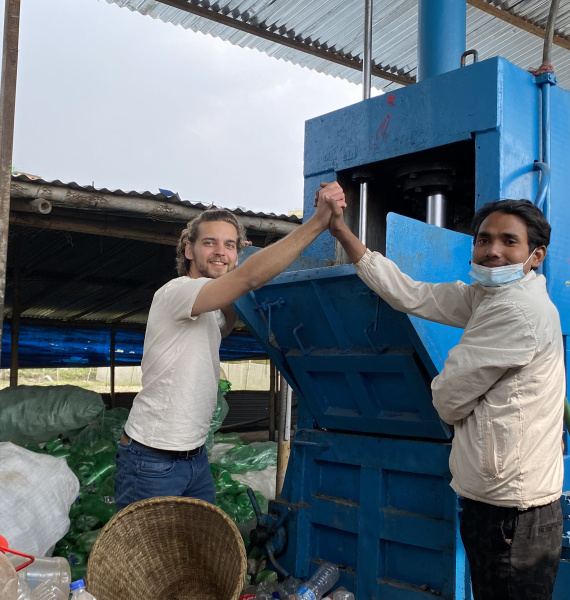
This is also why we decided to support NIDISI, a non-profit organisation in Nepal. With the slogan ‘Don’t waste the waste’, NIDISI achieves this change of mindset with its ‘Revalue’ project by giving value to what may seem worthless and reintegrating plastic into the value chain. In this way, plastic waste is perceived as a resource and not as waste. The Revalue project is committed to the sustainability claim of working against environmentally harmful plastic, to improve the living conditions of the people affected and to advocate for socially acceptable work.
Availability of PCR raw materials
Targets for recycled content are becoming increasingly ambitious. In addition to the 2025 Ellen MacArthur Foundation targets, the European Union expects 30% of raw materials used to be PCR by 2029, as part of the European Single-use Plastics Directive. PCR content is also increasingly being seen as a differentiating factor on the market, pushing brand owners to launch products with the highest PCR content technically possible. These two factors have caused a significant increase in the demand for PCR raw materials, and thus a considerable spike in the prices in recent years.
Downcycling
Unfortunately, high-quality recycled PET (rPET) is procured by other sectors such as the textile and automotive industries at a very competitive price. According to figures from Eunomia and Zero Waste Europe, 68% of PET bottles are downcycled, leaving only 32% on the original PET beverage bottle market. This means that the plastic beverage packaging industry will likely be unable to meet the target for recycled content, as the required quantity and quality of rPET is simply not available. Legislation at the European level should therefore ensure the promotion of closed-loop (bottle-to-bottle) recycling.